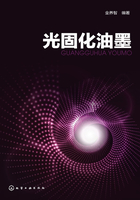
3.3 UV装饰性油墨
在包装印刷行业中,近年来利用UV固化技术,开发出一系列具有特殊装饰效果的UV网印油墨。这是由于在UV油墨印刷与固化过程中,通过控制UV油墨的组成、固化机理及固化速率的不同方式,可以产生很多种自然的、特殊的装饰图案,这些图案无论溶剂型、烘烤型或自干型油墨都无法产生。人们还利用油墨印刷过程中常会产生气泡、缩孔、疵点、皱纹、橘皮、晶纹等缺陷,人为地通过不同手段加以夸大,从而产生皱纹、磨砂、珊瑚、冰花等图案,具有很好的装饰效果,并发展成为新的UV网印油墨。这些具有特殊装饰效果的UV油墨组成了一系列的UV装饰性油墨。这些UV装饰性油墨广泛地应用于包装印刷,不仅提高了包装印刷的档次,而且成为高档烟、酒、茶、保健品、礼品、工艺品印刷包装和请柬、贺卡、挂历、名片、装饰材料印刷的重要材料。
UV装饰性油墨品种很多,大致可分为三种类型。
①外添加型。即油墨内添加了具有特殊效果的填料、颜料或助剂,印刷后油墨表面呈现特殊的装饰效果,如磨砂油墨、珠光油墨、发光油墨、香味油墨、发泡油墨等。
②化学转变型。油墨印刷后,表面看不到装饰效果,在光固化过程中,油墨发生化学或物理变化,表面形成皱纹、冰花、裂纹等图案的皱纹油墨、冰花油墨等。
③特殊印刷型。通过特制的网版,印刷出特定的效果图案,如折光油墨、水晶油墨、七彩油墨、立体光栅油墨等。
每一种UV装饰性油墨采用的工艺流程不同,所得到的装饰图案效果也不一样。通过控制印刷或光照条件,才能使所得到的装饰图案符合设计要求。
由于UV装饰性油墨主要用于烟、酒、茶、保健品、化妆品、请柬、贺卡等高档包装印刷,所以必须要做到以下几点。
①无味环保。不含有任何带有不良气味的成分,油墨在印刷过程中无气味,对印刷车间和包装车间没有污染。
②安全无刺激。油墨对人体皮肤无刺激,避免操作人员因不小心接触而造成皮肤过敏或灼伤,保障操作人员安全。油墨组分固化后不易发生迁移,以免污染产品。
③附着力好,耐刮性强。油墨对纸质承印物特别是通用的金银卡纸要具有极好的附着牢度及表面硬度,印品的耐刮和耐划伤性要好。
④高耐抗冲击性和柔韧性。鉴于印品在印刷后,往往还要经过压凸、模切等具有冲击性的后续加工工序,要求油墨层在印品上有较高的抗冲击性和一定的柔韧性。
因此在生产UV装饰性油墨时,要选择好低聚物、活性稀释剂和光引发剂,特别要选用无味、皮肤刺激性小的活性稀释剂和迁移性小、光解产物无气味的光引发剂。
3.3.1 UV折光油墨
UV折光油墨俗称激光油墨,是用于折光(激光)印刷的一种特殊油墨。折光实际上是指反射光而非折射光,所以折光印刷又称反光图纹印刷。折光印刷利用光的反射原理实现其特殊装饰效果,它采用光反射率高的材料,通常用金银卡纸、涂铝薄膜或镜面不锈钢等作承印物。
折光印刷常见的有传统的机械折光、激光折光和目前较为流行的网印折光3种。其实这3种方式的本质是一样的,都是通过压印将折光纹理图案复制到承印物表面。
机械折光是通过激光电子雕刻或腐蚀的方式将折光纹理图案刻在金属版上,然后用很大的压力将折光纹理图案转移压印到承印物表面。机械折光可采用圆压平或平压平的方式。圆压平方式适合大面积、大批量印刷作业;平压平方式适合局部小面积、小批量印刷作业。
激光折光的压印方式类似于机械折光,只是其折光印版纹理的形成要复杂得多。首先是激光器将折光图案信息记录在全息记录材料上,然后采用电铸的方法将折光纹理复制到刚性的金属模版上,形成非常致密的、人眼无法识别的光栅,将折光纹理图案转移压印到承印物表面。机械折光和激光折光不需要油墨,只需通过刚性的模版,利用压力将折光纹理压印至承印物表面,而网印折光要用到油墨,即UV折光油墨。
网印折光是将精细的丝网模版制版技术与先进的桌面排版制作技术相结合,制作带有折光纹理的网版,用网版印刷的方法印上UV折光油墨,便能在镜面金银箔卡纸上获得极其精细的多彩折光(镭射)的图案,这些有规律、凹凸状的图案在光的照射下能产生有层次的光闪耀感以及三维立体的独特效果。
由于传统的用压印方式产生折光(镭射)纹理的方法制版成本高,效果也不甚理想,所以折光印刷现在大多数采用网印印刷,使用UV折光油墨。折光印刷主要应用于高档烟、酒、茶、工艺品包装及请柬、挂历、贺卡等商品,印刷后不但能使包装商品光彩夺目、华丽富贵、立体感强,而且还具有一定的防伪作用。
折光效果是在某些具有金属质感的承印物表面进行加工,使之在各个视角上既有变幻的金属光泽,又有清晰明辨的立体图像的表面整饰加工工艺效果。产生折光效果的第一个条件是承印物表面具有金属光泽,最好是光泽达到一定的镜面反射效果;第二个条件是承印物表面印刷有折光纹理。折光纹理是由一系列规则平行的、等距的、具有几个不同角度的极细实线组成的纹理图案,如同心圆形折光纹理、平行线形折光纹理。
折光效果的形成是光线与折光纹理相互作用的结果。光线从各个方向射入印刷有折光纹理的承印物表面后,反射出来的光线由于受到折光纹理的影响,产生更多方向的反射,部分光线甚至产生干涉现象而强化反射效果,最终形成闪闪发光的折光效果。
折光印刷中折光图案精细复杂,它由几十条角度、弧度不同的线条通过同等距离的排列组成,其线条粗细在0.10~0.15mm,因此要求UV折光油墨具有高光泽、高分辨率和优良的触变性,保证网印后线条清晰。
UV折光油墨在使用时需提前一天放进车间,使油墨温度和生产车间的温度相同,因为温度的差异会使油墨的黏度发生变化,印刷效果也会不同。油墨在使用前必须充分搅拌,使油墨有良好的印刷适性,并能提高油墨的均匀度。印刷时可根据需要加入适量的稀释剂进行稀释。如果折光印刷图文面积较大,为保证质量,必须用高精度的网版印刷机来完成,小面积的可采取手工印刷方式。
使用UV折光油墨时应避免其和皮肤接触,若油墨粘在皮肤上,应立即用肥皂水冲洗。油墨保存不当或超过保质期将会使油墨特性发生改变,影响印刷后的效果。应避光、低温(18~25℃)、密封贮存,保质期6 个月。
网印折光方法简单,技术要求不高,虽然生产效率相对较低,防伪效果稍逊色于机械折光和激光折光,但折光效果也很强,对于小批量的产品来说平均成本低廉。因此,网印折光近年来发展迅速,受到许多中小企业的推崇,目前已经成为折光印刷的主要趋势。
UV折光油墨为无色透明油墨,不用颜料,实际上就是一种UV透明光油,它的制备见“3.17UV上光油”。
3.3.2 UV皱纹油墨
通常情况下,油墨在干燥时,若表面层与底层收缩不同,则会产生起皱现象。这种起皱现象本来是印刷中的缺陷,但如果有意识地突出和控制起皱,使其形成一种独特图纹的装饰效果,就可以使印刷品别有一番韵味,能产生这种起皱效果的油墨就是UV皱纹油墨。
网印UV皱纹油墨通常多用在光泽度很高的金卡纸、银卡纸等承印物上,也可印在有机玻璃、PVC片材、塑料薄膜上。油墨印刷后,先经过低压汞灯254nm UV照射,使油墨表层固化,内部呈半固化状态,表层UV油墨由于固化收缩,产生凹凸模样的纹路。然后,再通过中压汞灯UV照射,使UV油墨整体固化,就可以达到具有金属锤打效果或折皱的表面效果。其实皱纹漆早已存在,常涂装在电器设备或机器的外壳上,但它需要高温烘烤才能得到满意的皱纹效果,故此工艺无法应用于以纸为基材的包装材料上。而UV皱纹油墨巧妙地采取了UV油墨两次固化的工艺,利用UV油墨固化时体积收缩引起油墨层起皱,产生了特殊的装饰效果。由于UV皱纹油墨具有立体感强、豪华典雅、墨膜饱满和良好的视觉效果等特点,其应用已扩展到高档烟包、酒盒、礼品包装盒、保健品包装盒、化妆品盒、挂历、书本等领域产品包装的表面装潢印刷。
使用UV皱纹油墨产生的皱纹大小与丝网目数、网印墨层厚度有关,丝网目数越低,墨层越厚,皱纹越大;丝网目数越高,墨层越薄,皱纹越小。一般使用丝网目数100~200目为佳。
UV皱纹油墨的皱纹形成需经过起皱和固化两个阶段,首先经低压汞灯光照射表面形成皱纹,再通过中压汞灯光固化。皱纹大小除与油墨厚度有关外,与通过低压汞灯的速度也有关系,速度太快,无皱纹产生,速度太慢,表面已固化,也不会产生皱纹。通过控制传送带速度,改变低压汞灯与高压汞灯之间的距离,可确定最佳工艺参数。
UV皱纹油墨的性能要求见表3-19。
表3-19 UV皱纹油墨的性能要求

UV皱纹油墨是不加颜料的,实际上也是一种UV透明光油,它的制备见“3.17UV上光油”。
UV皱纹油墨使用要点如下。
①UV皱纹油墨使用前应充分搅拌均匀,一般无须稀释即可直接印刷。如确需稀释,可用UV皱纹油墨专用的光油(稀释剂)调稀,比例一般不超过5%。如需着色,可加相应的色浆调匀后印刷,但加入量一般不超过3%。不同系列及品牌的UV皱纹油墨一般不可相互拼混,以免发生不良反应影响印刷效果。
②对于某些附着性不好的承印物,可先用相应的透明油墨印刷,再印UV皱纹油墨,即可解决附着性问题。
③在批量使用前,应少量试用并充分确认符合材料与设备要求后才能批量使用。油墨应贮存于阴凉干燥处,用后盖紧密封,注意避免接触明火及高温。保质期一般为 1年。
④UV皱纹油墨通常用于网印,要根据需要达到的皱纹效果来选择不同目数的丝网。网印中对印刷品的精度要求越高,选用的丝网目数越高,反之,则选用的目数越低。网目数越高,产生的皱纹效果越小,反之则越大。因此,在UV皱纹油墨网印中,根据实践经验,一般选用100~200 目的丝网,如果印刷设备精度很高,则可以适当地选择目数高一些的丝网。
⑤选择合适的网距。网距小于5mm时,图像能够完全呈现在承印物上,而当网距超过 5mm时,随着网距的增加,呈现在承印物上的图像有丢失现象。根据实践经验,网距的设定范围是 2~5mm比较合适。
⑥选择合适的绷网角度。根据网印的实践经验,绷网角度为45°时,龟纹最严重,绷网角度是60°、75°时,龟纹也比较严重,绷网角度为30°时,龟纹较轻,而绷网角度为 0°、10°、20°、25°时,印刷品基本上没有产生龟纹,因此,绷网角度的范围可选择小于30°。
⑦注意调整印刷速度和控制刮刀角度。印刷速度的变化不会带来印刷品质量的变化,只能改变油墨起皱花纹的大小。印刷速度快,花纹就小;印刷速度慢,花纹就大。同样,刮刀角度的变化也不会改变印刷品的质量,仅改变花纹大小。刮刀角度小,花纹小,反之,花纹就大。因此,在紫外线固化时,以出现最佳花纹效果来调整最佳的印刷速度和控制刮刀角度。
⑧要注意控制油墨的引皱和干燥速度。引皱速度过慢,印刷品无法起皱。实验证明,当引皱速度小于 14m/min 时,油墨基本上无法起皱;当速度达到 14m/min 以上时,油墨均会起皱。因此,一般生产中可选择 14~20m/min 的引皱速度。
⑨注意墨层的厚度和油墨的颜色对UV固化的影响。由于网印的墨层厚度很大,当油墨太厚时就会影响固化效果,所有影响印刷墨层厚度的因素都会影响固化效果。对墨层厚度有影响的因素有丝网目数、张力、感光胶厚度、胶刮硬度、胶刮刃口的锐利度、刮印角度、刮印速度、压力等,在印刷中要注意控制这些因素。此外,颜料对网印UV油墨也有较大的影响,不同颜色、不同厚度的UV皱纹油墨的UV固化效果也有差别,这主要是由于各种颜料对光线吸收、反射及油墨中颜料含量不同。一般来说,白色、黑色、蓝色、绿色较难固化,红色、黄色、光油、透明油易固化。利用光引发剂的特点,可以通过选择光引发剂的种类、降低颜色密度,使不同颜色的UV皱纹油墨在同一固化条件下达到固化参数的一致;墨层的厚度应该通过改变网版的参数、胶刮的硬度和刮印速度等方法调整,保证油墨的快速固化要求。
UV固化要求UV固化机加装引皱装置,光源为20~40W 低压UV灯,功率在60~100W,UV引皱装置与UV固化灯之间的距离不低于 1.2m,否则印刷后的产品未经UV引皱装置引出皱纹而被UV灯固化,花纹无法引出,也无法达到皱纹的效果。UV固化灯的功率不低于3kW ,传送带的速度视印刷光固效果而定,一般在18~25m/min。UV引皱装置的功率与传送带的距离直接影响产品的花纹,UV引皱灯的功率大,传送带的速度要快,反之,UV引皱灯的功率小,传送带的速度则要慢。
3.3.3 UV仿金属蚀刻油墨(磨砂油墨)
UV仿金属蚀刻印刷就是利用UV仿金属蚀刻油墨中含有杂质而产生的疵点对光线产生散射,这本来是印刷中应尽量避免的缺陷。但如果在油墨中加入大量“杂质”,用仿蚀刻丝网印刷把这些小颗粒漏印于具有金属镜面光泽的金银卡纸上,就可产生犹如光滑的金属经腐蚀、雕刻式磨砂等处理的特殊效果。UV仿金属磨砂印刷所产生的特殊视觉效果的光学原理是:印有UV仿金属磨砂油墨的图文部分在光的直射下,油墨中的小颗粒对光发生漫反射形成强烈的反差,犹如光滑金属表面经磨砂产生凹陷的感觉;没有油墨的部分因金银卡纸的高光泽作用,产生镜面反射而有凸出的感觉,仍然具有金银卡纸金属般的光泽度。它能使承印物具有金属般的光泽度和似蚀刻后的浮雕立体感,产生磨砂、哑光及化学蚀刻的效果,使印刷品显得高雅庄重、华丽美观,大大提高了印刷品的装饰档次及艺术欣赏价值。
仿金属蚀刻印刷制作方法有以下三种。
压砂:即利用凹凸不平的钢模,在高压下加热定型,压出磨砂效果。
平面喷砂:在要磨砂的图案部分,先用腐蚀液进行哑光处理,待干燥后,用预制的具有类似喷砂玻璃面的凹凸纹的模具压制图案区,同时加热,使压制的凹凸纹热熔定型,起模后得磨砂图案。
印砂:这是使用最广泛的一种仿金属蚀刻印刷方法,它是直接利用丝网印刷在具有镜面光泽的材料上网印UV仿金属蚀刻油墨,获得磨砂效果。
UV仿金属蚀刻油墨是一种粒径为15~30μm的无色透明单组分UV网印油墨。油墨墨丝短而稠,其中添加颗粒直径为15~30μm的“砂粒”,印刷后可在光照下形成漫反射,产生磨砂效果。所谓的“砂粒”实际上都是无色透明的塑料细颗粒,如聚丙烯、聚氯乙烯、聚酰胺等塑料粉末,满足颗粒大小在15~30μm就可用。为了反映出承印物的固有光泽,UV仿金属蚀刻油墨一般是将低聚物、活性稀释剂、光引发剂、填料等多种材料搅拌成浅色透明糊状,也可加入颜料制成彩色蚀刻油墨,但不能使用遮盖力强的颜料。性能优越的UV仿金属蚀刻油墨首先要具有良好的颗粒分布及立体感,蚀刻效果好,印刷后才能产生令人满意的艺术效果;还要求附着力及柔软性优良,否则在烟、酒盒等进行轧缝时会发生爆裂,严重影响产品质量;还需要固化快、存放期长、手感好,不能太毛糙,否则在烟标等包装生产线中容易发生轧片现象。此外,印刷烟标及食品包装盒的油墨还必须具有低气味性,保证油墨符合食品卫生和环保绿色印刷的要求。UV仿金属蚀刻油墨在配料时添加的各种助剂、材料要充分搅拌均匀,为了减小印刷后油墨在承印物膜面的流平性,要少用或不用流平剂,以促进凹凸粗糙面的形成。还有,在配方设计中要保证仿金属蚀刻油墨具有良好的触变性、适宜的附着力,根据不同的承印物和设备环境等因素调整控制好油墨黏度。
UV仿金属蚀刻油墨性能要求见表3-20。
表3-20 UV仿金属蚀刻油墨性能

在采用网印UV仿金属蚀刻油墨印刷时,丝网的选择是至关重要的,选择的丝网目数应与油墨砂型的粗细程度相匹配,如果油墨砂型比较粗,颗粒度大,应选择较低目数的丝网,其丝网的孔径较大,可使油墨中砂粒通过丝网漏印到承印物上,否则会使部分砂粒残留在网版上,造成印刷品上的砂粒稀少,出现花白现象,导致蚀刻效果差。并且随着印刷的进行,油墨砂粒不断堆积,网版上的油墨黏稠度逐渐增大。如果砂型较细,颗粒度小,则可选择较高目数的丝网。一般油墨砂粒直径在15~30μm,选用的丝网目数在150~250目即可,具体情况可根据实际使用经验来选择。
为使UV蚀刻印刷有良好的视觉效果,承印物的选择也很重要,一般选择具有金属镜面效果和高光泽的材料。材料的平滑度也很重要,若平滑度低印刷适性就不高,油墨附着性就差。蒸镀有铝箔的卡纸、铝箔都可以印刷,但以金银卡纸最为理想。
在印刷中要熟悉和掌握UV仿金属蚀刻油墨的印刷适性,一般来说,UV仿金属蚀刻油墨在使用全自动网印机进行大批量高速生产时会出现问题,往往在印几千张或上万张后,仿金属蚀刻油墨就不能完全密实地铺展在丝网上,导致仿金属蚀刻效果不均匀;UV仿金属蚀刻油墨太稀或相溶性不好,则易导致跑边、露底等。为了避免这些问题,首先要使用符合质量要求的金银卡纸,因为对于一些质量相对较差的金银卡纸,UV仿金属蚀刻油墨会溶解金银卡纸上的金银色,严重时甚至把金银色全部溶掉,使整个印品发白。要解决这个问题,在设计油墨配方时,就必须全盘考虑各种原材料的组成,不选用分子量小、溶解性能强的活性稀释剂,以避免金银卡纸掉色。当然,增大UV光源强度,缩短印品从印刷到固化的时间,对于克服印品发白的弊病也有一定的效果。
如何使UV固化油墨产生哑光效果?可以通过添加微粉蜡或无机哑光粉等来获得。蜡是油墨中很常用的组分,用以改变油墨的流变性、改善抗水性和印刷性能,使印品网点均匀完整。微粉蜡一般为合成的聚乙烯蜡和聚丙烯蜡,分散于UV网印油墨中,固化成膜时,由于蜡与树脂体系存在不相容性,故游离而浮于固化墨膜表面,使光泽度受到影响,形成哑光效果。这种哑光效果有柔软的手感和蜡质感,但由于蜡粉仅仅是浮于印膜表面而形成消光作用,又因蜡质本身强度较低,抗刮伤能力差,所以效果大多不够理想。如果改用气相二氧化硅、硅微粉、滑石粉等无机填料组分,由于浮于膜层的表面的能力差,故难以获得哑光磨砂效果。
对添加硅粉消光剂的UV油墨,可以采用分步辐照的方法来获得哑光磨砂效果。先对湿墨层用较长波长的光源辐照,因其对膜层较有力的穿透效果,可使下层油墨基本固化,墨层表面层虽然光能相对较强但受氧阻聚的干扰,上表层固化较差,在墨层内形成下密上疏的结构,有一种迫使填料上浮的作用力,再加上无机填料(硅粉)与有机交联网络的不完全相溶性,无机粒子就会被迫向固化状况较差的表层迁移,聚集到墨层表面。此时再用波长较短、能量较高的光源辐照墨层,使油墨表面层彻底固化,这样便可得到明显的哑光磨砂效果。
3.3.4 UV冰花油墨
UV冰花油墨是一种特殊的UV透明油墨,它采用网印工艺,将油墨印在具有镜面感的镀铝膜卡纸上,经紫外线照射固化,承印物表面将出现晶莹剔透、疏密有致的冰花图案,在光的照射下发出耀眼的光彩,能使包装更加新颖别致。冰花油墨一般用于商品包装、礼品、贺卡、标签等产品的表面装饰。但由于UV冰花油墨产生冰花所需的UV照射时间太长、生产效率太低、耗能过高、纸张易变形等缺点,多数还只用于小批量的印刷,未能在包装业中大量使用。UV冰花油墨也可印刷在透明的基材上,如玻璃、透明亚克力、透明PC等,常被用来反印正看;也可印刷在具有反光效果的底材上,如镜面不锈钢、钛金板、镜面氧化铝板等。
UV冰花油墨是无色透明油状液体,加入专用色浆,还可以印刷各种彩色的冰花图案 。也可以先印好透明的彩色UV油墨,光固化后再叠印冰花油墨,获得彩色的冰花图案。UV金属/ 玻璃冰花油墨是专门为玻璃及镜面金属底材而开发的,硬度高,有优异的附着牢度,耐水性强。为了使玻璃上的透明冰花图案具有金属闪光效果,在冰花表面印刷一层UV镜面银油墨,从玻璃或透明塑料薄膜的反面观看时,冰花就具有金属感,冰花油墨好像是印在镜面金属上。
UV冰花的形成机理是:当UV冰花油墨受到紫外光照射时,会发生两种反应,一种是主反应,即光化学聚合/交联反应,促使油墨固化,同时产生体积收缩,由于配方中树脂的官能度较高,所以冰花固化膜既硬又脆。墨层的收缩和固化过程是不同步的,也是不均匀的,其结果必然造成应力集中,导致固化膜开裂,形成许多类似于冰面被敲击的裂纹图案,即冰花图案。UV冰花纹理是自然形成的,非人为所致,具有自然美的特点,艺术感很强。另一种是副反应,即空气中氧气产生的氧阻效应,也就是说氧气会阻碍油墨的进一步固化,对固化不利,尤其是与空气直接接触的冰花墨层表面很难固化。
UV冰花的形成过程分为三个阶段:大裂纹的产生;小冰丝的形成;冰花墨层的干燥。当印刷好的冰花油墨进入紫外光照射区域时,油墨表面慢慢地会出现一层白雾状的固化层,本来完全透明的涂层变得不那么透明了,并逐渐形成纵横交错的裂纹图案,就好比天空中出现了很多条闪电轨迹。大裂纹的产生一般需要中等强度的紫外光照射20~40s。随着大裂纹逐渐变深,墨层表面的白雾逐渐退去,有的地方变得透明,有的地方半透明,墨层变成了分布着许多大裂纹的透明层。一眨眼的工夫,大裂纹的边沿又出现了无数细小的冰丝,彼此朝着一个方向快速增长,直到碰到对面的冰丝为止,冰丝的形成时间很短,一般为5~10s。如果此时用手触摸油墨表面,黏糊糊的还未固化。冰丝的粗细与密度决定冰花图案的立体效果。冰丝越密、越细,冰花的反光和折射效果越明显,立体感越强,但透明度较差;冰丝越粗,密度越低,冰花墨层的透明度越好。大裂纹和小冰丝形成后,冰花墨层就需要用强紫外线照射使之快速干燥,否则美丽的冰花图案会因为氧阻作用变得模糊不清。仔细观察UV冰花图案,尤其是用高倍放大镜观看时,会发现冰花是由许许多多的大小裂纹组成的,有的裂纹大又长,有的裂纹短而细(简称为冰丝)。大的裂纹相互交叉并连接在一起,冰花图案的大小是由大裂纹所围合的面积决定的,面积越大,冰花越大,反之冰花越小。UV裂纹决定冰花的大小,冰丝决定立体感,只有充分了解UV冰花的形成过程和影响因素,才能生产出立体感强、透明度高、大小合适的UV冰花装饰产品
底材的性能(颜色、透明度)对冰花的形成也会产生很大的影响。底材颜色越深,冰花固化得越慢,冰花就大,颜色浅的地方,冰花就小。在其他条件不变的情况下,通过改变底色也可以控制冰花的肌理效果。
要想得到稳定的冰花,还必须保持光照区域温度的稳定。因为冰花的形成过程受温度的影响很明显,温度越高,墨层中的氧气的溶解速度越快,溶解的氧气量越多,固化速度就会越慢,冰花就会越大。所以印刷冰花油墨,夏天生产很正常,天气一冷就遇到了麻烦,最好的解决方案就是印刷车间的温度相对稳定。
冰花油墨印刷的均匀性,不但影响产品的颜色深浅,而且决定着冰花图案的大小。印刷冰花油墨时,一般选用200~260目丝网版,网目低,墨层厚,冰花就大;反之,冰花花纹就小。冰花油墨的黏度较大,网印时应放慢刮印速度,使墨层均匀一致,否则生产出来的产品不光颜色深浅不一,冰花大小也不一样。
印刷UV冰花油墨时,环境温度应尽量保持稳定。温度高,油墨黏度小,气泡消失得快,印刷墨层较薄,光照后形成的冰花花纹较小;温度低,油墨黏度大,印刷时易产生气泡,墨层较厚,形成的花纹较大。因此,印刷环境温度的波动会直接导致冰花图案大小的变化,从而影响产品的批次稳定性。建议印刷环境温度控制在20~30℃较佳。
UV冰花光固机比普通的光固机长很多。标准的四灯UV冰花光固机,网带/滚轮宽度2m,灯管发光区长1.95m,前三只UV灯功率12kW,最后一只UV灯功率16kW,灯管总功率52kW,机器宽度2.2m,灯箱长度5m,总长7~8m。UV冰花光固机的每只UV灯作用不同,并且灯距可调。前三只灯产生冰花,最后一只用于固化油墨。普通的三灯UV固化机长度一般只有2.5~3.5m。
UV冰花光固机温度控制要求较高,风机多。不管春夏秋冬,灯箱内的温度要求控制在35~55℃。
3.3.5 UV珠光油墨
UV珠光油墨是将云母珠光颜料加入UV油墨中而制得的一种具有珠光幻彩效果的特种油墨。珠光颜料为无机颜料,由云母晶片组成,外层包裹为具有高折射率的金属氧化物,如二氧化钛、氧化铁,利用云母片的反射或闪光效应,使颜料表面具有珠光色彩。云母是天然硅酸盐,大多数云母矿不适合作珠光颜料,只有密度为2.7~3.1g/cm3、硬度为2.0~3.0的单斜晶系的白云母 KAl3O10Si3(OH)2才适合制作云母珠光颜料。将透明的白云母晶体处理成片状颗粒后,用化学方法将二氧化钛等金属氧化物涂覆于云母片表层,既可提高云母表面的耐光、耐候性,还可通过调节色膜厚度来获得各种干涉色。
表3-21为二氧化钛膜的膜厚与色相的关系,表3-22为云母钛的粒度与二氧化钛的附着力关系。
表3-21 二氧化钛膜的膜厚与色相的关系

表3-22 云母钛的粒度与二氧化钛的附着力关系

在应用中,将珠光颜料均匀分散在涂层中,而且平行于物质表面形成多层分布,同在珍珠中一样,入射光线会通过多重反射、干涉达到珠光效果。这种珠光效果不同于普通“吸收型”颜料和“金属”颜料,它所表现出的色彩是丰富而具有变化的。人眼在不同的视角观察同一点时,光泽会不同;人眼在同一视角看不同点时,光泽也会不同。总的看来,珠光就像是从物体内部或深层发出来的光芒。
珠光颜料随其颗粒大小的不同在使用中表现出不同的效果。总的说来,颗粒越大,闪光度越高;颗粒越小,对底色的覆盖力越强,而闪光度降低。
改变涂布在云母内核上的金属氧化物的厚度或种类,也会带来不同的色彩变化。把珠光粉应用于包装领域,将获得更多意想不到的华丽享受。
另外,珠光颜料的优势在于它良好的物化特性,耐水、耐酸、耐碱、耐有机溶剂、耐热,300℃无变化,不导电,耐光性极好,无毒,对皮肤和黏膜无刺激,不会引起过敏反应。
使用金属离子还可以得到彩色的珠光颜料,不同的金属使珠光颜料呈现不同的颜色,如使用含Bi、Sb、As、Cd、Zn、Mn、Pb等化合物的产品具有稳定的色彩。另外,在云母钛表面沉积Au、Ag、Cr、In、Sn、Ni、Cu、Ge、Co、Fe或Al的氧化物,可增强颜料对光的反射,提高珠光效果,见表3-23。
表3-23 金属与珠光颜料色彩的关系

表3-24介绍了云母钛不同粒度时的光泽,表3-25介绍了云母钛的色相和膜厚、包覆率之间的关系,表3-26则介绍了云母钛的几何学厚度和色相的关系,表3-27介绍了默克公司的珠光颜料。
表3-24 云母钛不同粒度时的光泽差异

表3-25 云母钛的色相和膜厚、包覆率的关系

表3-26 云母钛的几何学厚度和色相的关系

表3-27 默克公司的珠光颜料品种

注:表中黑斜体标出的产品为推荐用于印刷的产品。
UV珠光油墨可印在几乎所有的材料上,如纸张、塑料、金属、玻璃、陶瓷、织物等,特别是在纸张、针织品上应用较多。
珠光颜料属于无机颜料,本身颗粒较大,虽然具有透明性,但是珠光颜料对紫外线反射也最强。所以要根据珠光涂层的效果来调节颜料的加入量,加入量过多,不仅影响油墨黏度,更会影响油墨的光固化速度。
珠光颜料为片状结构,对剪切力非常敏感,大的剪切作用会破坏珠光效果,所以油墨制作时,颜料的分散不能使用常规的三辊研磨机、球磨机和砂磨机,只能使用高速搅拌机分散,而且必须慢速分散搅拌,以免破坏云母片状结构。珠光颜料几乎可以和所有天然和合成的树脂相混合,而且润湿性和分散性都比较好,特别是在聚酯树脂和羟基丙烯酸树脂中。
珠光颜料在加入油墨连接料之前应首先进行润湿。润湿用的溶剂应与油墨体系相适应。良好的润湿可以使珠光颜料均匀地分散到油墨连接料中,这是获得优质珠光印刷效果的基础。同时,润湿也能克服珠光颜料在分散时的“起尘”现象。由于珠光颜料具有良好的分散能力,在低黏度体系中一般使用低速搅拌即可很好地分散。
UV珠光油墨中加入的珠光颜料颗粒都会对紫外线发生吸收、反射或散射,使紫外线很难到达油墨层底部,影响UV珠光油墨的固化,尤其是底部更难固化。因此制备UV珠光油墨必须要选择合适的、光引发效率高的、有利于深层固化的光引发剂,如ITX、TPO和819等,有时还要配合使用增感剂EDAB等。
珠光颜料可提供一个崭新的、个性化的色调效果,它既可以单独使用,也可与透明的常规颜料合用,另外底层涂料的颜色与之叠合,又会有更令人惊喜的色彩产生,其装饰效果的丰富性几乎可以无限延伸。干涉色系列珠光颜料既可单独使用,也可同其他传统色料同用,干涉色会随视角改变而产生多种效果。
①“珠光白”效果,银白系列珠光颜料既可单独使用,又可同其他传统色料一起使用。需要注意的是色料应该为透明性的,而且添加浓度不能超过3%。由于该珠光颜料透明性高,金属光泽效果很强。
②“珠光幻彩”效果,干涉色系列珠光颜料既可单独使用,也可同其他传统色料同用,干涉色会随视角改变而产生多种幻影色彩,只有一种混合方式不可取,即将不同的干涉色颜料相混合,因其结果是暗淡的灰色。
③“珠光金及金属色”效果,这种珠光颜料不同于传统的铜粉或铝粉颜料,除一般的金色以外,它还提供了更引人入胜的多种光泽。主要的色彩有黄金光泽、紫铜、青铜和红金色。如果加少量碳(0.001%~0.05%),可以产生独特的金色或铜色效果。银灰色则可以通过将珠光银白颜料涂于黑的底色上,或将其同少量炭黑在油墨中混合而产生。
与常见的油墨颜料不同,珠光颜料以下几个特点对于印刷结果的影响非常重要,因此,在油墨制备和使用时,绝对不能忽视。
(1)颜料的易损性
珠光颜料由二氧化钛(或其他金属氧化物)包覆云母而成,呈脆弱的薄片状结构,容易损坏。在珠光油墨的配制中,不要采用大剪切力或者有研磨功能的分散装置。
(2)颜料的颗粒度
普通有机颜料颗粒的尺寸是0.2~0.7μm,炭黑更小些,为0.02~0.08μm,而常用的云母钛珠光颜料(F级)尺寸达到了25μm,厚度为0.2~0.5μm。必须对印刷中的相关参数进行调整,不然珠光颜料的转移将受到很大影响。
(3)颜料的排布
这与薄片状颜料结构有关,当颜料在油墨涂层中分布得均匀,而且多数颜料颗粒同承印物表面呈平行排列时,得到的光泽最好,否则就会大打折扣,因此应该注意油墨转移后的流平性,流平性好才能保证颜料薄片排布的质量。
(4)颜料的透明性
珠光效果主要来源于入射光线的折射和干涉,如果油墨涂层的透明度低,原本充足的光线就会被吸收而损失掉。在选用油墨连接料或光油的时候,要选择透明度尽可能好的材料,所以一般制备UV珠光油墨时,常用透明的UV光油作连接料。
3.3.6 UV香味油墨
人们在印刷上除了追求视觉美的效果外,在嗅觉上有所突破也是一个方向,香味印刷随之产生。香味印刷最早是在印刷油墨或纸中加入香料以得到香味,这种方法简单,但不易持久。后来由于发明了微胶囊技术,将香料封入微胶囊内,并制成油墨进行印刷。由于香料被微胶囊封闭,徐徐散发出来,故印品能持久飘香。在UV香味油墨固化后用手指轻轻摩擦,即可闻到浓郁的香味。香味印刷主要应用于杂志、广告、传单、说明书、明信片、餐单、日历等方面,也可用于纺织物印花。
UV香味油墨是一种微胶囊油墨,是在UV油墨中添加了微胶囊而制成的一种特种油墨。微胶囊技术是20世纪中期发展起来的一门新技术。它是在物质(固、液、气态)微粒(滴)周围包覆上一层天然高分子或合成高分子材料薄膜,形成极微小的胶囊。微胶囊具有许多特殊性能,它能够储存微细状态的物质,并在需要时释放出来,还可改变物质的颜色、形状、质量、体积、溶解性、反应性、耐久性、压敏性、热敏性及光敏性。因此微胶囊技术广泛应用于医药、食品、化妆品、洗涤用品、农药、化肥、印刷等行业。微胶囊技术与油墨生产制造技术结合为印刷油墨的开发提供了新思路,不仅促进油墨新品种的开发,如香味油墨、发泡油墨、液晶油墨等,还产生了许多印刷新工艺,提高了包装印刷品的附加值。
微胶囊的直径一般在微米至毫米级,粒径在2~200μm,若粒径<1μm称为纳米胶囊。包在微胶囊内部的物质称为囊心,囊心内的核心物质可以是液体、固体或气体,可以是单核也可以是多核。微胶囊的外皮即由高分子成膜材料形成的包覆膜称为壁材,或称为外膜、包膜,囊壁厚度为0.5~150μm,可以是单层,也可以是多层。
微胶囊囊壁所用材料一般为天然高分子化合物或化学合成高分子材料。以天然物质提取而成的,主要有明胶、阿拉伯树胶、淀粉、蜂蜡、骨胶蛋白、乙基纤维素、阿戊糖、甲壳素等,这类材料黏度大、易成膜、致密性好、无毒或极微毒,但力学性能较差。由化学方法合成的,如聚乙烯醇、聚苯乙烯、聚酰胺、聚氨酯、聚脲、环氧树脂等,这类材料力学性能好,但生物相容性较差。这些物质的最大特点是具有一定的成膜性,且在常温下比较稳定,囊壁厚度一般在0.2μm 至几微米。使用时应根据囊心内核心物质的黏度、渗透性、化学稳定性、吸湿性、溶解性等因素来确定选用何种高分子材料作壁材。
微胶囊的制备方法主要分为化学法、物理化学法和物理法3类。化学法主要是利用单体小分子发生聚合反应,生成高分子成膜材料并将囊心包覆,常见的为界面聚合法、原位聚合法和乳液聚合法等。物理化学法主要是通过改变条件,使溶解状态的成膜材料从溶液中聚沉出来,并将囊心包覆形成微胶囊,有代表性的是凝聚法分离技术。物理法主要是利用物理和机械原理制备微胶囊,此法具有设备简单、成本低、易于推广、有利于大规模连续生成等优点,比较成熟的有空气悬浮被覆法、喷雾干燥法、挤压法、多孔离心法等。
图3-7为凝聚法制备微胶囊的示意图,该制备技术应用了胶体化学中的凝聚现象的原理来制备微胶囊。

图3-7 凝聚法制备微胶囊的过程
①首先将微细的心材分散入微胶囊化的介质中;
②再将成膜材料倒入该分散体系中;
③通过某种方法,将壁材聚集、沉积或包覆在分散的心材周围;
④微胶囊的膜壁是不稳定的,尚需用化学或物理的方法处理,以达到一定的机械强度。
微胶囊的功能较多,在印刷方面主要有降低挥发性、控制释放、隔离活性成分、形成良好的分离状态等功能。UV香味油墨主要利用微胶囊的降低挥发性和控制释放的功能,由于香料被胶膜包裹,香味徐徐散发,其香味保存时间最长可达一年;也有的香味微胶囊只有在紫外线照射、氧气流通、加热、湿度变化等环境因素催化作用下才会互相反应,产生香味物质,这样就可避免印刷品在一般情况下的无效逸散,更可延长香味散发的时间。UV香味油墨的香味的散发受温度的影响,25℃以下时散发慢,随温度升高散发速度加快。理想状况下,微胶囊在印刷过程中不易破裂,但用手触摸印好的成品就会散发出香味。这是因为印刷压力一般在微胶囊能承受的压力范围内,一旦形成印刷品,由于胶囊与空气接触,囊壁或多或少会氧化,从而导致其能承受的压力变小,此时用手触摸便散发出香味。
由于微胶囊化油墨的颗粒相对较粗,要求印刷的墨层要厚一些,并且印刷时不能使用较大的印刷压力,否则会导致微胶囊破裂,所以对印刷方式有一定的要求,通常采用丝网印刷比较理想。因为丝网印刷具有一些优势,如印刷墨层可厚达100~300μm,其厚度比微胶囊颗粒大,既可对微胶囊起到保护作用,又可以得到其他印刷方式不能得到的印刷效果,它完全能胜任含微胶囊油墨转移的特性。另外,丝网印刷适合各种材料特性和形状的承印物,为微胶囊技术的广泛应用奠定了基础。在选择丝网目数时要清楚丝网孔宽与油墨中微胶囊颗粒体积的关系,一般丝网网孔的宽度至少为油墨中微胶囊(或填料)颗粒直径的3~4倍。UV香味油墨中使用的香味微胶囊一般直径在10~30μm,因此制成UV香味油墨后,采用丝网印刷,丝网网目选用200~300目较适宜。
由于含微胶囊颗粒丰富的UV香味油墨较难表现画面的色彩和层次,故尽量不要选择原稿层次非常丰富、清晰度要求很高的画面作原稿。印刷时要注意控制油墨的黏度,含微胶囊的油墨在印刷之前要进行黏度调整,稀释剂要适当,使微胶囊颗粒能顺利通透而不影响其质量。黏度过高,油墨不易通过丝网版转移到承印物上,造成印刷困难,但黏度太低会造成印迹扩大,影响印刷质量,甚至造成废品。在印刷过程中印刷速度不能太快,以免刮墨刀摩擦产生热量使温度升高,导致微胶囊颗粒破裂。为了确保油墨能顺利地透过丝网孔而转移到承印物上,印刷压力的调节很重要,印刷压力过大也会造成微胶囊破裂。除了注意刮墨后版面上的油墨是否均匀外,对采用不同壁材的微胶囊,在印刷时应结合印刷效果运用不同的印刷压力。当进行多套色叠印时,要结合实际情况具体安排,因为不是每一种色都带有微胶囊颗粒的,所以要合理安排带有微胶囊颗粒的色墨的色序。若把含有微胶囊的色墨放在最后一色印刷,可避免后面进行印刷时破坏微胶囊体;但放在前面印刷时,也可因后来油墨叠加上去而起到保护微胶囊释放的作用。因此要结合实际情况合理安排。
香味油墨的香料应满足以下要求:
①微胶囊破裂后,香料与空气接触的机会多,因此香料要有一定的抗氧化能力;
②水溶性香料含有水分,为避免香料对油墨产生较大影响,应选用油溶性香料;
③香料挥发度要小,稳定性和持久性要好;
④香料应为液态;
⑤香料化学性质不能受油墨影响;
⑥在满足其他条件的情况下,成本要尽可能低;
⑦胶囊壁材要具有疏油性和一定的抗氧化能力。
UV香味油墨网印工艺要点如下所述。
①香味油墨网印丝网的选择。应尽量采用尼龙单丝平织丝网,因尼龙单丝平织丝网的纤维表面圆滑,具有高弹性和柔软性,油墨通透性好。丝网的网孔宽度至少应大于油墨中颜料颗粒直径的3~4倍。
②香味油墨网版印刷要点。网印的油墨黏度应为2Pa·s左右,所以香味油墨在印刷前要进行黏度调整,使之达到所需黏度。印刷速度不能太快,以免刮墨刀摩擦产生热量而使温度过高,导致微胶囊颗粒破裂(这里所说的印刷速度是刮墨速度)。印刷压力不能太大,网印过程中除了要注意刮墨后版面上的油墨是否均匀外,还要观察微胶囊是否破裂,嗅有无香味飘出,这样,边试边印,调节压力。进行彩色阶调印刷时,还应考虑色序问题,含微胶囊的色墨最好放在最后印刷,以避免后续印刷时破坏微胶囊体。
3.3.7 UV发泡油墨
UV发泡油墨是一种在承印物上形成立体图案的装饰性油墨,由于印刷图案具有立体感,表现出自然的浮雕形状,似珊瑚、似泡沫、似皱纹,花纹自然、美丽、奇特,除能增强装饰艺术效果外,还可以赋予盲文阅读的特殊功能。UV发泡油墨通过网印方式在纸张或织物上印刷,可获得图文隆起的效果,应用日益广泛,在塑料、皮革、纺织品等包装物上进行印刷,其外观手感、透气、透湿、耐磨、耐压、耐水、色泽等方面都具有独特之处。
UV 发泡油墨也是一种微胶囊油墨,采用微胶囊技术制备而成,在微胶囊中充入发泡剂,经加热处理,发泡剂释放气体,使微胶囊体积增大到原体积的5~50倍,将此种微胶囊制成UV发泡油墨。由于微胶囊是空心的,所以硬度、耐刮性不是很好,使用时尽量不要用硬的东西刮擦,这是发泡油墨的缺点。
常用的发泡剂的性能见表3-28。
表3-28 常用发泡剂的性能

发泡印刷设计的注意事项:
①发泡油墨经加热,体积膨胀5~50倍,色调浓度变淡,设计时应考虑彩色配搭的协调性。
②发泡后的墨层表面粗化,变得不透明,不能像一般油墨那样多色套印成色。必须按设计色要求采用各自专用色。
③因发泡后体积增大,大面积实地图案表面易缩皱,发泡不均,损坏艺术效果,设计时对大面积实地图案采用80%粗网点或用有微细间隔的线条代替,要为发泡留有充填的余地。
④发泡印刷对于0.2mm以下的细线条和过于细密的图文效果不好。最好不要全部采用发泡油墨印刷,只对需要强调的部分使用,其他部分采用普通油墨印刷。印刷时将发泡油墨印刷安排在最后较妥。
⑤在UV 发泡油墨中添加专用UV色浆,可以改变图案颜色。加入专用的发泡剂,可控制油墨花纹的大小和疏密,用同一块网版,可以印出几种不同的发泡图案,大大增加了产品艺术装饰效果。
发泡印刷的应用范围很广,按承印材料类别可归纳为纸张类、布品类、皮革类、金属类、玻璃类、防滑材料及缓冲材料等。
发泡印刷在包装装潢、书籍装帧、书刊插页、盲文刊物、地图、墙纸、棉纺织品等印刷中有着广阔的应用前景。
3.3.8 UV发光油墨
UV发光油墨是一种在透明油墨中加入发光材料制备出的特种功能油墨,目前已经获得了广泛的应用。一般的发光油墨采用热固化油墨掺杂发光材料制成,采用加热固化的方式制备发光制品,在UV油墨中使用有一定的难度,这是由发光材料的特殊性决定的。发光材料即长余辉蓄光型发光材料是一种粒径在10~60μm的无机粉体材料,在特殊条件下甚至还有更大的粒径,这种粉体材料具有一定的体色并且不透明,在实际使用中需要印刷一定的厚度才能体现出较好的发光效果,这些问题给UV固化发光油墨的使用带来一定的难度。
将发光粉加入油墨中是制备发光油墨的一种通用方法,过去都是将热固化油墨与发光粉混合制备发光油墨。随着UV技术的发展,将发光粉与UV油墨结合制备UV发光油墨已经逐渐被广大印刷厂商采用,尤其是在发光标牌的制作上用UV发光油墨代替热固发光油墨具有相当大的优势。采用网版印刷技术进行UV发光油墨的印刷是制备发光标牌的一种常用方法。
①发光粉选择。UV发光油墨在网版印刷中要考虑发光粉的选择,发光粉的基本要求是亮度要高、粒径适中。粒径大无法从网版中漏下,粒径小印刷厚度不够,需要增加印刷次数才能达到厚度要求,费工费时,一般采用50~80μm的发光粉较合适。稀土发光粉是浅黄绿色的,因此选择制作标志牌的底材以蓝色或绿色为宜。
②网版制作。发光标牌一般都要求发光层印刷得较厚,因此通常采用的是80目涤纶单丝的网版,这样发光粉可以通过网版,同时印出的发光层也比较厚。在制版中要考虑一般标牌产品中如一些地名标牌往往同一图案不会连续印刷多次,在这种情况下可选用低档耐油性感光胶,可节省成本。
③预涂底层。在印刷发光层之前需要印刷一层白色底层,发光层印刷在白色底层上。印刷底层是印刷发光油墨的必要步骤之一,在基体表面预涂底层,将有助于提高发光油墨的发光性能。使用不同颜料的底层对油墨发光性能的影响不一样,加入二氧化钛的白色底层最有利于提高发光油墨的发光性能,这是因为白色底层可使透过油墨层的入射光以及发射出的荧光更充分地反射,最大限度地发挥发光油墨的作用。
这里需要注意的是UV发光油墨需要在白色底层上具有很好的附着力,否则固化后发光墨层容易脱落,一般选用白色PVC油墨,这是因为大多数UV油墨在PVC油墨层上都具有很好的附着力,因此可避免发光层从标牌上脱落的现象。
④在多次印刷固化时,要注意层间附着力。采用UV发光油墨时要注意一个很重要的问题,标牌制作中往往需要发光层达到一定的厚度,这时需要进行多次印刷才能达到厚度要求。由于UV油墨是在印刷一遍后立即进行固化,固化后的表面光滑,在进行下一次印刷时是在前一层的基础上进行的,此时需要UV油墨在每层间都具有较好的附着力,不能出现分层现象。因此在UV油墨的选择上要特别注意层间附着力的问题。
长余辉蓄光型发光材料与UV油墨结合用于印刷中需要注意以下问题。
①长余辉蓄光型发光材料是一种无机粉体材料,发光材料密度较大容易沉淀,因此使用前需要进行搅拌,同时发光材料容易与铁锈、重金属等发生反应,因此在分散研磨过程中不宜采用金属棒,不适合在金属容器中保存,否则会导致材料变黑,影响使用效果。容器选择玻璃、陶瓷、搪瓷内衬、塑料容器为宜。
②发光油墨成膜后,发光吸光功能是由发光材料的颗粒来实现的。由于光线通过的要求,将发光材料粘接在一起的树脂应该有较好的透光性,无遮盖力,所以选树脂、清漆要以无色或浅色透明度好为宜。
③发光材料的含量越高,辉度就越亮,但是为了使发光材料与涂饰制品有合适的附着力,树脂的比例最低不能少于10%。当然,树脂的比例越高,发光涂层的平滑度和光洁度就越高。因此,发光材料的用量一般为总质量的20%~60%,或为容积的10%~35%,或根据发光亮度的要求确定发光材料的用量。
④UV发光油墨在网印中要考虑发光材料的选择,发光材料的基本要求是亮度要高,粒径适中。粒径大无法从网版中漏下,粒径小印刷厚度不够,需要增加印刷次数才能达到厚度要求,浪费时间,采用20~80μm的发光粉较合适。发光材料颜色较多,制作标志产品一般选用浅黄绿色的发光材料。
⑤制作工艺上,发光材料不能研磨,不能使用三辊研磨机,配制发光油墨,只能使用高速分散机或搅拌机。具体方法是将树脂或清漆放入容器中,加入助剂,开动搅拌器,在慢速搅拌状态下依次加入防沉剂、发光材料。加完发光材料后提高转速,直至发光材料均匀分散在物料中,过滤即可得到产品。
⑥不能使用重金属化合物作添加剂。
要注意网版目数的选择。一般的发光材料由于粒径比较大,需要较小目数的网版,通常采用100目以下的网版印刷效果比较好。印刷后产品的固化程度也对产品的最终质量产生影响,测试固化是否完全的方法有以下四种。一是用铅笔硬度仪进行测试,一般达到3~4H,可以认为油墨已经完全固化。二是用滴溶剂的方法进行测试,还要测试耐溶剂性,将丙酸滴在印品表面20min 后,如没有变化证明已经完全固化。三是压强法试验,即将棉纤维放置在印刷品表面,用底面光滑的500g砝码压在棉纤维表面2~3min,然后拿开砝码,若棉纤维不粘在印刷品表面证明已完全固化。四是划格试验法,采用划格器用力在印刷品表面划十字,然后用胶带粘划十字的表面,如果没有粘下来油墨,说明固化完全并且固化后油墨层的附着力比较好。
3.3.9 UV珊瑚油墨
在印刷时,涂层中有气泡是十分头痛的事,但是如果在涂层中有大量气泡相互聚集,这种无规律的连续堆积与无气泡平滑部分在一起形成珊瑚状纹路图案,这种图案可以产生特殊的装饰效果,网印UV珊瑚油墨就是利用该原理制成的。这种油墨又可称为珍珠油墨,当墨层较厚时,气泡聚集在一起形成珊瑚状的花纹;较薄时,形成小珍珠粒状,也别有风味。网印UV珊瑚油墨多用于各类挂历、酒包、化妆品盒的表面装潢印刷。在使用珊瑚油墨时,应注意按所需的花纹选择丝网目数,如要印成粗珊瑚状,丝网用得粗些,刮刀口钝些;如要印成小珍珠状,则可用250~300 目的丝网。此外,还可以调整油墨印刷后等待通过UV机的时间来控制珊瑚花纹的大小,通常情况下,立即通过UV机,花纹清晰有序;等待时间越长花纹会越大越模糊。
3.3.10 UV立体光栅油墨
立体印刷是根据光学原理,利用光栅板使图像记忆立体感的一种印刷方法。立体印刷较平面印刷来说,其核心技术就是光栅技术。光栅是立体印刷形成立体影像的观景器,是立体彩色印刷技术的基础。
光栅是一层由条状柱面透镜组成的光学材料,是指依照人类视觉原理规则地排列于透明平面材料上,形成对图像信息的分割与聚集合成的一种光学元件(特殊透镜)。将这种特殊透镜有序排列在由立体印刷工艺印制的承印物上而形成透明材料体。
印刷光栅按特殊透镜形式分为平面透镜光栅、柱面透镜光栅和球面透镜光栅三种。目前,立体印刷成像均采用柱面透镜光栅,其是当前应用最多也是最成熟的光栅。
柱面透镜光栅成像是根据透镜折射原理实现图像的立体再现。柱面透镜光栅是由许多柱面透镜组成的透明塑料板(片),其表面的光栅线条由许多结构参数和性能完全相同的小半圆柱透镜线形排列组成,其背面是平面,为柱面透镜元的焦平面,每个柱面透镜元相当于汇聚透镜,起聚光成像的作用。因此,可以利用在不同视点上获取的二维影像来重建原空间物体的三维模型。用它制作的立体图像不需要背光源或立体眼镜就能正常观看,其成像原理如图3-8所示。

图3-8 柱面透镜光栅板成像原理示意图
随着UV印刷技术的广泛应用以及光栅材料的改进,开始在光栅材料背面直接印刷反向光栅图像制作立体印刷品,实现了印刷与光栅复合成像同步完成。此工艺不仅省去了光栅复合工序,而且由于采用UV油墨固化技术,胶印油墨能瞬间固化,确保印刷的精度和效率,是当前立体图像印刷的主要工艺及方式,UV胶印技术构成现代立体印刷的基础。近年来,出现了立体光栅油墨技术,其工艺是先在纸面上按传统平面彩色印刷要求印刷光栅图像,然后用丝网印刷方式在图像上印刷光栅油墨,最后通过在线光栅热压成型技术制成立体光栅印刷品。该技术与UV快速固化工艺相结合,可实现全自动流水线生产,是高线数光栅立体印刷工艺的发展方向。随着现代印刷技术多样化发展及立体印刷产品应用领域的不断拓展,喷墨打印技术和数码印刷技术也将在立体印刷领域得到应用。
“胶印+光栅复合”的立体印刷技术在印刷之后需将印刷图像与光栅板进行复合,光栅复合成像主要有3种方式。
①平压贴合法。采用平压机,在柱面透镜成型的同时将聚氯乙烯薄膜贴附在承印物上,实现印刷品与光栅板复合成像。
②辊压贴合法。将卷筒式聚氯乙烯薄膜充分加热,然后让其与承印物重叠,并从冷却阴模与压辊之间通过,在柱面透镜成型的同时与其进行加压贴合,实现印刷品与光栅板复合成像。
③先成型后贴合法。由平压机将成型的硬质柱面透镜光栅板用黏合剂贴附在印刷品表面,实现印刷品与光栅板复合成像。目前使用较多的是先成型后贴合的方法。
光栅参数包括光栅线数、光栅厚度、光栅视距、光栅透光率、光栅偏差值等。目前光栅常用线数为62线/in、75线/in、100线/in和141线/in。光栅厚度直接影响所能表达的立体图像的景深范围。光栅表达景深范围的能力用聚焦景深系数来表示,通常75线/in以上的光栅聚焦景深系数为2~3;30~75线/in的光栅聚焦景深系数为2~4;30线/in以下的光栅聚焦景深系数为3~5。光栅视距与光栅线数有一定对应关系(如表3-29所示)。光栅透光率越高,图像越清晰。光栅偏差值越高越好,以保证达到图像栅距与光栅栅距的精确匹配。
表3-29 光栅线数与视距关系

注:1in=2.54cm。
立体印刷光栅材料以塑料为原料,主要有PET(聚酯)、PP(聚丙烯)、PVC(聚氯乙烯)三种。通常制作光栅板的方法有两种。一种是热压成型法,注塑成型是热塑性光学透镜加工的重要方法,光栅板是塑料透镜的一种,也是人们使用的光学元件的重点部件。用光栅板模具与塑料片密合后加热加压,使塑料制成凸球面型柱镜面光栅条纹。另一种是网版印刷法,用透明的UV立体光栅油墨直接在塑料片上网印出光栅条纹,再经紫外线照射固化,即可得到光栅板。网印光栅工艺不仅速度快、成本低,而且可以局部印刷光栅条纹,使图像达到局部立体化,可以生产出整幅画面既有立体图像又有平面图像的产品。
网印光栅就是把光栅上的条纹当作图文来进行印刷,图3-9为光栅板上条纹的结构示意图。

图3-9 光栅板上条纹的结构示意图
网版印刷墨层厚可达30~100μm,因此覆盖力强。近年来开发出厚版胶,网版厚度可达800~1000μm。由于光栅观景面对厚度的要求特别高,如200线的细光栅的厚度为0.3mm,100线的厚度要在0.4mm以上,所以,从形成油墨层厚度的能力来分析,印刷光栅时网印技术是在线光栅(局部立体印刷)制作的首选方法。
UV立体光栅油墨是在UV网印光油材料基础上,为了适应在线印刷光栅的特殊需求而特制的一种油墨。它除了满足网印UV油墨要求,还必须满足立体光栅UV油墨的以下三点要求:
①超厚度。一般UV网印墨层厚度在30~60μm,而立体光栅UV油墨要求墨层厚度达到200~500μm,并应在瞬间UV固化干燥,依靠油墨层堆积达到需求厚度是不科学的。
②可塑性强。这里所指的可塑性是指网印后,未经UV照射固化定型前,UV墨层只结膜未定型,可接受一定外压力作用而产生任意变形的特性,这时可模压成型。这是实现在线光栅制作的关键。模压成型后即可UV照射固化定型,其可塑性随之消失。
③高度透明性。因为光栅是形成立体图像的观景器,必须是一种光学透镜元件,所以必须既要有良好的光学表面性又要有极强透明度,否则难以观察到立体图像。
UV立体光栅油墨配方是在网印UV上光油墨的基础上调配而成的,网印UV上光油是一种无色透明的油墨,在其中加入一定量的高级透明的松香粉末,经搅拌均匀即可使用。如松香40%+普通上光油 18%+网印UV上光油42%混合均匀,就可调制成UV立体光栅油墨。由于油墨尚未UV照射固化,此时利用光栅模具热压成型,油墨中松香粉因受热速溶而体积膨胀,在其表面形成一张由条状柱面镜组成的透明塑料薄片,再UV固化,就制成立体光栅。
近年来,随着立体印刷品制作方法的发展,UV印刷光栅的方法得到了较快发展,该工艺是将立体图像直接印刷在柱面透镜光栅的背面,一次完成立体图像,此工艺不仅省去了复合工艺,而且立体效果更佳,是立体印刷工艺的发展方向。
3.3.11 UV锤纹油墨
这是一种新型的光固化美术油墨,网版印刷后涂层自然收缩,在被涂装物体表面形成一层具有独特花纹的固化膜,这种花纹与铁锤敲打铁片所留下的锤纹花样类似,锤纹凹凸起伏、立体感明显。印刷在镜面金属上,锤纹还有金属闪烁的光泽。
UV锤纹油墨既有无色透明光油,也有各种金属颜色,如浅金色、古铜色、银色等。无色透明光油适用于网印各种高光泽底材,如印在镜面金银卡纸上,生产装饰品、工艺品等,印刷在镜面金属板材上,生产各种锤纹效果的标牌、面板、天花板等。花纹的大小与丝网目数的高低直接相关,网目越高,墨层越薄,花纹越小;反之,花纹越大,网目以300~420目为佳,固化膜有优异的耐磨性、耐溶剂性,附着力佳。印刷好的产品即可直接光固化,不能停放太久,否则花纹会发生变化,会造成批量产品花纹不一致。
3.3.12 UV水晶油墨
UV水晶油墨使用低目数(40目、60目、80目)网版印刷,UV光固化后,可获得光亮透明、平滑柔韧且具有强烈立体感的上光效果。在水晶油墨中加入1%~5%的镭射片、七彩片及金属片,搅拌均匀后进行网印,可获得金属闪烁效果。UV水晶油墨适用于高档烟酒、挂历、书刊封面、贺卡等包装印刷。
水晶油墨无色无味、晶莹剔透、印后线条不扩散,透明似水晶。印刷品图文具有立体透明的水晶状效果、浮雕般的艺术感,典雅别致。如果加入适量的镭射片、闪光片、特殊效果金属颜料,即可获得各种立体闪烁装饰效果。该油墨可广泛应用于各种水晶标牌、装饰玻璃、书刊封面、挂历、水晶画、烟酒包装盒、标牌及盲文等商品的印刷。
水晶油墨一般是采用特殊UV树脂及助剂制成的紫外线固化油墨。它无色无味、晶莹剔透、不挥发,固化后不泛黄,印后线条不扩散,透明似水晶。水晶油墨有硬型和柔韧型,油墨外观呈透明浓浆状,如果加入适量的闪光片、特殊效果金属颜料,即可获得各种立体闪烁和金属装饰效果。印刷网版必须是低目数的厚膜丝网版,否则达不到立体水晶的效果。如采用低目数的(40~80目)厚膜丝网版印刷,可以获得高凸起、立体透明的水晶状效果,使印刷品图文具有浮雕般的艺术感,典雅别致。印刷时尽量采用原墨印刷,不同系列及品牌的油墨一般不可相互拼混,以免发生不良反应,油墨使用前应充分搅拌均匀。气温较低时,会变得较浓稠,如印刷困难,可加入少量专用的水晶油墨稀释剂调匀后印刷,不可随意用其他稀释剂,否则会影响图文的印刷质量和立体效果等。
3.3.13 UV凹印和柔印装饰性油墨
UV装饰性网印油墨品种繁多,性能单一,有的使用麻烦,生产能力低,为此人们又设法采用凹版印刷和柔版印刷来印刷装饰性图案,从而开发了UV装饰性凹印油墨和UV装饰性柔印油墨。这是我国自行研发的包装印刷技术和装饰性油墨,不但具有完美的装饰效果,而且具有很好的防伪效果。
①凹版印刷法印刷装饰性油墨。主要通过用电雕刻法或激光雕刻法对装饰性图案进行制版,同时研制了与其配套使用的装饰性凹印油墨,并在凹版印刷机上安装了UV固化设备来实现。凹印所产生的图案是由制版时的网点及线条的排布、大小及深浅来决定的,只要在一个印版上制作具有不同效果的磨砂、折光、冰花、皱纹或珊瑚等图案,用一种油墨就可印出不同的装饰性图案,使印品更富有艺术性。鉴于凹印的印刷一致性好,只要一个印版,用同一油墨和同一种纸,即使印上百万张,其统一性也很好,故具有很好的防伪功能。凹版印刷速率快,墨层厚,难以彻底固化,为此UV装饰性凹印油墨除了采用新型活性高的低聚物、活性稀释剂和光引发剂来巧妙组合,还添加了能提高固化速率和克服氧阻聚的纳米材料,制备了印刷速度高于150m/min的UV装饰性凹印油墨。
②柔版印刷法印刷装饰性油墨。采用数字激光柔性版技术制作柔性版,传墨用网纹辊,尽量达到可转移10μm以上的墨层厚度,用光学性能好(高折射率或高散射性)的材料制作UV油墨,经组合使用,印品不但装饰效果完满,而且还有很好的防伪效果。由于柔印工艺的限制,所印的油墨层较薄,如需印刷一些具有特殊效果的厚墨层,可用辊筒式网印机进行印刷,为此又开发了适用于辊筒式网印机的UV装饰性网印油墨。
3.3.14 UV装饰性油墨参考配方
(1)UV银白色珠光油墨参考配方
EA(EB605) 40
PUA(EB264) 17
TPGDA 15
TMPTA 10
184 2
PBZ 4
Tego UV680 1
Foamex N 1
BYK3510 0.3
银白色珠光粉(欧克1112) 10
(2)UV紫色珠光油墨参考配方
EA(EB608) 40
PUA(EB265) 15
PO2NPGDA 8
(EO)3TMPTA 20
ITX 2
907 3
Tego UV680 1
Foamex N 1
BYK3510 0.3
紫色珠光粉(欧克2220) 10
(3)UV深红色珠光油墨参考配方
EA(EB745) 55
PUA(EB220) 5
DPGDA 8
TMPTA 10
TPO 2
ITX 1
907 3
Tego UV680 1
Foamex N 1
BYK3510 0.3
深红色珠光粉(欧克7312VRA) 10
(4)UV珠光油墨的参考配方

(5)UV水性珠光丝网油墨参考配方
PUA水性树脂(固含量30%) 60
聚氨酯类增稠剂 1
珠光颜料 18
pH 值调节剂(二甲基乙醇胺) 2
成膜助剂(乙二醇丁醚) 4
消泡剂TEGO Foamex843 0.7
流平剂Ciba EFKA3570 0.3
水 10
2959 2
819DW 2
(6)UV水性珠光丝网油墨参考配方
PUA水性树脂(固含量55%) 50
聚氨酯类增稠剂 2
珠光颜料 10
pH 值调节剂(二甲基乙醇胺) 1
成膜助剂(乙二醇丁醚) 3
消泡剂BYK028 0.8
流平剂(德谦公司的Levaslip 468) 0.2
水 30
2959 1
819DW 2
(7)UV网印磨砂油墨参考配方
双官能度脂肪族PUA(611A-85,含15%TPGDA) 80
(PO)2NPGDA 10
PETA 10
BP 2
184 1
活性胺(Etercure 6420) 5
消泡剂(Foamex N等) 4
平滑剂(Eterslip 70) 0.2
磨砂颗粒(5378) 20
(8)UV网印发泡油墨参考配方
双官能度脂肪族PUA(611B-85,含15%HDDA) 50
改性EA(6231A-80,含20%TPGDA) 20
(PO)2NPGDA 10
(PO)3GPTA 10
PETA 10
184 1
BP 2
活性胺(Etercure 6420) 5
稳定助剂 1
流变调节剂 5
(9)UV网印皱纹油墨参考配方
双官能度脂肪族PUA(611A-85,含15%TPGDA) 25
双官能度脂肪族PUA(622A-80,含20%TPGDA) 20
TMPTA 15
(EO)3TMPTA 20
HDDA 10
BP 4
活性胺(Etercure 6420) 10
消泡剂等(Foamex N) 5
平滑剂(Eterslip 70) 0.2
(10)UV荧光油墨参考配方
丙烯酸共聚物溶液(MAA/MMA/EA/BA,固含量45%) 132
四乙二醇二丙烯酸酯 40
369 3
荧光颜料(Y,Gd)BO3∶Eu3+ 140
低熔点玻璃黏结料 3
丁酮 36
(11)UV防伪油墨参考配方
EA 100
DPGDA 9
TMPTA 6
其他稀释剂 30~35
651 2~5
二苯胺 0.3
稀土荧光配合物 1~3
(12)UV雪花油墨参考配方
白色微胶囊(MFL-81GCA) 25
EA 10
PUA 25
丙烯酸-2-乙基己酯 25
TMPTA 7
DETX 5
分散剂(685) 3