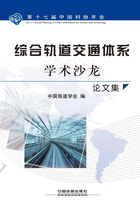
城际动车组齿轮箱体的铸造技术与质量控制
徐贵宝,周 峰,马俊成
(南车戚墅堰机车车辆工艺研究所有限公司,江苏常州 213011)
摘 要:介绍了城际动车组齿轮箱箱体的结构设计、低压铸造工艺设计与优化,以及变质处理、精炼除气和热处理等工艺方法,研制的动车组齿轮箱具有内部质量好、实物力学性能高的优点,确保了产品的安全可靠性。从工艺装备、过程控制、质量检测等方面阐述了产品的质量控制措施,保证生产过程质量稳定性。
关键词:机械制造工艺与设备;城际动车组齿轮箱;低压铸造;制造工艺;质量控制
1 引言
齿轮箱是高速列车的动力传动装置,是列车的核心部件之一,其作用是将牵引电机的扭矩有效地传递到车轴而使动车组加速,或者是将车轴的转矩传递给牵引电机发电而使动车组减速,其工作性能的好坏直接影响到动车组运行的可靠性和安全性。箱体是该传动装置的关键零件,其结构和性能与传动装置的可靠性密切相关,因此箱体的设计与制造非常重要。
国外城际动车组齿轮箱设计使用具有机械性能优良、制造工艺性好、重量轻的高强度铸铝合金齿轮箱体[1]。
我国运行的动车组主要为引进消化吸收国外技术的CRH2、CRH3系列及自主研发的CRH380系列,其驱动装置全部依赖国外进口,主要供应商是德国的弗兰德、福伊特和日本的东洋电机等。其中,德国福伊特是动车组齿轮箱领域老牌资深的供应商,有40多年的铁路齿轮箱生产经验,并且也向欧洲高铁ICE供货,但其最近供应的中国高铁动车组的齿轮箱,连续出现箱体裂纹、热轴故障等多起问题,严重影响到行车安全和运行效率。而东洋电机供应的我国动车组齿轮箱,也曾经发现有的箱体加工表面存在较为严重的针孔现象,有一定比例的箱体在规定的探伤部位存在超标的缩孔缩松缺陷,影响到传动装置的使用可靠性。
我国动车组齿轮箱驱动装置主要依赖国外进口,进口的齿轮箱不仅价格昂贵,而且在性能上不能满足我国动车组的发展需要,极大地制约了中国动车组关键零部件的技术发展和产业化进程。
为了打破国外技术的垄断,戚墅堰所从2010年开始了动车组齿轮箱国产化研究,通过四年多的技术攻关,自主研制了中国南车CRH6-160及CRH6-200城际动车组,现实了批量装车;国产化CRH380A齿轮箱驱动装置,通过了30万km的装车运行考核;同时,完成了中国北车CRH380B齿轮箱的研制,正在进行装车考核。
国产化箱体的内在质量和性能指标达到甚至优于国际先进水平,但外观质量还有待进一步提升。本文介绍了CRH6城际动车组齿轮箱体的先进铸造技术和质量控制方法。
2 箱体结构设计
2.1 选材
戚墅堰所从1994年开始进行了高强度铝合金齿轮箱的铸造技术研究,已成功应用于城轨列车及大功率机车等齿轮箱体的制造,累计生产约10000多套,产品质量稳定可靠。
作者简介:徐贵宝,男,教授级高工,主要从事铸造凝固模拟、材料与工艺的研究,以及铸造技术及质量管理工作。
结合这些生产实践经验,根据城际动车组齿轮箱对材料性能的要求,参考进口齿轮箱的成分范围,选择力学性能较高、铸造性能优良,同时具有较好抗氧化和抗腐蚀能力的AlSi7Mg0.3作为城际动车组齿轮箱材料。该材料的化学成分及力学性能如表1及表2所示。
表1 齿轮箱材料化学成分范围

表2 齿轮箱材料力学性能

2.2 静强度计算
CRH6城际动车组齿轮箱体结构设计为整体箱体与上盖组成,箱体前部设置了安全托以防止齿轮箱掉落。
在箱体最低处设有排油孔,从而便于箱体内润滑油的排出,在满足外部接口及限界的情况下,尽量加大箱体内腔空间及外形尺寸,以便于更好的润滑及散热降温。将齿轮箱三维模型导入到有限元分析软件中,划分网格并施加边界条件,计算几种典型工况下的箱体静强度,各种工况下最大应力计算结果如表3所示,图1和图2分别为最大扭矩时电机反转和正转时箱体Von Mises应力云图。
表3 在不同工况下CRH6城际动车组齿轮箱体最大应力值(MPa)

通过计算得出:在电机正转时,3种工况下的箱体最大应力都出现在电机侧小轴承座法兰外圈与吊挂部位及安全托部位筋板连接处;而在电机反转时,3种工况下的箱体最大应力都出现在箱体中间筋板车轮侧倒圆角处及电机侧小轴承孔法兰内圈与箱体内壁连接处。
在3种工况下箱体的最大应力都小于材料AlSi7Mg的屈服极限220MPa,箱体结构强度满足安全运用要求。
将小轴承座法兰外圈与吊挂部位筋板连接处定义为齿轮箱关键部位,在进行箱体铸造时,需重点关注该部位铸造缺陷及力学性能。

图1 电机反转时箱体Von Mises应力云图

图2 电机正转时箱体Von Mises应力云图
3 箱体铸造技术
3.1 铸造工艺设计与优化
日本及欧洲等动车组齿轮箱的生产,一般采用潮模砂、树脂砂或覆膜砂等造型工艺,使用重力铸造方法成型,铸件的外观质量很好,而内在质量从工艺上来说不容易得到保证,但由于其操作过程控制细致严格,工艺规范执行到位,因此铸件内在质量也能得到控制。
3.1.1 工艺方案设计
在工艺技术路线的选择上,吸收国外的先进经验,采用了国内外较为先进的低压铸造成型技术,铸件在压力作用下结晶凝固,可以提高铸件的补缩效果,铸件组织均匀、偏析少、致密度高。所以铸件的气密性、耐压性都得到提高,力学性能比一般重力铸造可提高10%左右,这对于齿轮箱更有明显的效果。
本工艺采用树脂砂和覆膜砂相结合的造型制芯方法,使得铸件尺寸精度高,操作过程相对简单。采用计算机控制自动化浇注,减轻了工人劳动强度。采用低压铸造,使铸件工艺出品率达到75%以上,比重力浇注工艺出品率高10%以上。
铸造工艺设计特点:选择HALF分型面,采用平做立交的方案,便于操作;设计开放式浇注系统,其比例为∑直浇道:∑横浇道:∑内浇道=1:1.5:2.3。
通过浇注系统实现由下向上的整体压力补缩,采取多个内浇口同时注入,分散热节减少针孔倾向。采用多冷铁工艺消除缩孔缩松或针孔缺陷,确保关键部位的内在质量和力学性能。
3.1.2 工艺模拟优化
使用凝固模拟技术对CRH6城际动车组齿轮箱体铸造工艺进行优化分析,大大缩短了铸件的试制周期,保证了产品的内在质量。
如图3所示,从充型模拟结果中看出,低压铸造充型过程平稳,避免了金属液产生翻卷、冲击和飞溅,减少了气孔、夹砂和非金属氧化夹杂物等铸造缺陷。

图3 铸件充型约50%的温度场

图4 铸件凝固约70%的温度场
从图4凝固温度场来看,铸件顺序凝固补缩良好,内部质量得到保证。
通过模拟分析改进了工艺:在顶部放置发热冒口,建立起由上向下的重力补缩,解决局部厚大部位的缩松问题;将一些冷铁改为铬铁矿砂替代,避免因冷却强度过大而阻碍补缩通道,同时有利于提高铸件外观质量。应用该工艺试制的齿轮箱经过射线探伤和实物解剖,测试结果完全满足技术要求的规定。
3.2 变质与精炼工艺
3.2.1 变质处理
采用Sr长效变质剂进行变质处理。这是国外使用较多的一种高效变质方法。其优点是Sr变质具有长效性且重熔性较好,氧化烧损小,不腐蚀炉衬,不污染环境,操作方便[2]。
目前,Sr变质基本取代了传统的Na变质。本文试验了Sr对AlSi7Mg0.3合金性能的影响,发现合金的极限抗拉强度和相对延伸率随Sr含量的变化规律呈抛物线形,即先逐渐增加后逐渐减小,如图5所示。
值得注意的是,当熔体中的氢含量大于某个临界值时,过多的Sr会增加针孔产生倾向,即Sr变质促使了针孔的形核和生长。因此,选择Sr含量的控制范围为0.02%~0.04%。
3.2.2 精炼除气
精炼过程非常重要,减少铝液中的氧化夹杂和含氢量,可有效地减少针孔产生倾向。采用FOSECO精炼除气站对转运包中的铝液进行精炼及除气,除气时间要求达到30min以上。
除气机的转速为300~800RPM,氮气压力:0.2~0.4MPa,流量:10~18L/min。使用真空测氢仪,根据密度当量法对除气过程进行控制。密度当量法测氢方法:取两个铝液样,分别在大气压状态下和在真空度为80mbar的状态凝固,测定两铝样的密度依次为ρatm和ρ80,用以下公式算出铝样的密度当量值DL:
DL=(ρatm-ρ80)/ρatm×100%

图5 抗拉强度和延伸率随Sr含量的变化

图6 浇注过程加压曲线
在齿轮箱浇注前,规定铝液密度当量DL应小于2%,ρ80≥2630kg/m3才能使用,且铝液必须在2h内使用完毕,否则重新精炼除气。
3.3 浇注工艺
低压铸造中,正确地选择和控制浇注工艺参数是保证获得合格铸件的关键。本文通过大量试验研究,制定的加压曲线如图6所示。
浇注温度控制在690~710℃。铝液的最大上升速度约为30mm/s,能够保证充型过程平稳[3]。确定保压压力为0.075MPa,这样既能保证铸件的致密度,又能避免产生机械粘砂。保压时间为720s,在保证铸件补缩良好的情况下,使金属液尽量多的回流。
3.4 热处理工艺
铸态AlSi7Mg合金组织较粗大,存在着枝晶间偏析及针状或片状的金属间化合物,所以一般不能直接使用,必须通过热处理工艺,改善其组织状态,得到所需要的力学性能[4]。目前AlSi7Mg材料广泛采用T6热处理工艺。本文研究了T6-A热处理工艺,适用于力学性能和产品尺寸稳定性要求较高的铸件。
淬火温度535±5℃,保温9h,将水温设定成60±15℃,转移时间控制在30s以内,时效温度200±5℃,保温5h。
图7和图8分别是采用T6-A热处理工艺材料的100倍及500倍金相组织形貌。可以看到,采用T6-A热处理工艺的合金中共晶硅多数为细小颗粒和短棒状,颗粒细小,分布较为均匀。

图7 T6-A热处理工艺(100×)

图8 T6-A热处理工艺(500×)
4 箱体的实物质量
研制的齿轮箱经过X射线探伤检测,铸件关键部位内部质量满足JISH0522:1969质量等级2级的要求,表面质量符合JISZ2343规定的相关要求。
按照技术要求对箱体进行实物解剖,测试了箱体14个部位的力学性能和10个部位的冲击吸收能量,检测结果全部达到技术要求的指标。同时还解剖了一套东洋公司的齿轮箱,对其进行了同样的检测,两者的平均值如表4所示。
表4 国产齿轮箱体与日本东洋箱体实物取样性能比较

对比发现国产箱体抗拉强度与箱体的相当,但屈服强度、尤其是延伸率和冲击韧性都比东洋箱体的数据高。
箱体的外观质量与国外箱体相比,还存在一定差距,主要原因是操作过程如造型制芯、冷铁摆放、涂料涂刷、打磨等做得不够细致,工人的外观质量理念没有国外的意识强,工厂管理水平还有待提高。
目前正在研究采用机器射芯、流涂或喷涂等方法取代手工操作,或使用金属型铸造,这将很大程度的提升外观质量。
按照试验大纲,对齿轮箱进行静强度试验、空载和加载试验,试验结果证明齿轮箱箱体及其驱动装置均满足试验大纲要求。
5 质量控制
一个优良的铸造工艺方案,如果生产过程不能执行到位,仍然不能获得优质的铸件。因此,加强过程控制、创新管理理念对提升产品质量也至关重要[5]。
5.1 重视工艺装备
工装对铸件质量影响很大,这往往被忽视。为了确保动车组齿轮箱产品的质量,落实了如下措施:技术人员所提供的工装设计资料不仅包括图纸、验证/验收要求,还包括工装的RAM/LCC分析资料、风险评估等,制作前需进行方案评审,验证合格后应将其登记造册,并于生产中对其进行管理和控制;对模具、冷铁、砂箱等工装进行编号;冷铁采用精密铸件;工装必须认真仔细进行周检和记录。
5.2 强化过程控制
以精益生产的理念建立生产过程质量管理制度,按照IRIS国际铁路联盟标准进行过程管控,通过工艺纪律检查、目视化管理、QC小组活动、“自检、互检、交检”制度真正落实、精益改善合理化建议、质量考核等措施,成功地保证了高铁齿轮箱生产过程中的质量稳定。具体措施如下:
首先从原材料开始,严把进货检查关;
造型制芯工序:每天开工前需进行工装检查,严格按照作业指导书进行操作,实行冷铁配送制度和型腔零修补制度,从源头上控制质量;
涂料工序:采用两遍涂料工艺,确保型腔耐火度,提高铸件表面质量;
合箱工序:建设了高铁齿轮箱专用合箱车间,在合箱前进行砂型质量检查,不合格的型芯不得使用,在梅雨季节增加铸型烘干工序,防止砂型吸潮;
熔炼工序:回炉料使用前应先去除表面的锈迹、泥沙等污物,熔炼工具应将表面油污、脏物等清除干净,涂刷防护涂料,并进行烘烤,防止针孔的产生;
除气浇注工序:采用FOSECO在线测氢仪对铝液含气量进行监测,浇注时实时观察低压浇注曲线;
清理打磨工序:开箱清砂时不允许击打铸件本体,使用专用切割机进行浇冒口切割,不同铸件部位使用专用打磨工具,以确保产品外观质量;
热处理:使用专业热处理炉和专用工装对齿轮箱进行固溶时效处理;
机械加工:先进行划线检查,并且先加工定位基准面,避免尺寸不合格品向下流转,及时反馈加工信息给铸造单位。
5.3 加强质量检测
对于动车组齿轮箱,为了保证铸件质量,确保使用安全,除了进行成分性能和射线探伤等常规检测外,加强了如下检测:
1)实物硬度;对每只齿轮箱在不同的位置进行本体硬度检测,并做好记录。
2)外观检测:把每一只齿轮箱毛坯放到专用检验台上,对外表和内腔表面质量进行仔细检查,并进行渗透探伤检测。
3)成像检测:每套齿轮箱都采用9MeV射线加速器进行实时DR成像检测,检查铸件所有内部缺陷。
4)气密性检测:对每套齿轮箱合箱进行0.1MPa~0.15MPa气压试验。
6 结论
对动车组齿轮箱设计计算、低压铸造工艺、变质和精炼技术、热处理工艺等各方面进行了深入的研究,形成了一整套试验数据,核心技术上实现了自主创新,达到了世界先进水平。
从工艺装备、过程控制、质量检测等方面采取有效措施,制定了详细的质量控制制度,创建了动车组齿轮箱制造技术平台,确保了产品的质量稳定。
通过对齿轮箱箱体的一系列检测,表明齿轮箱各项指标均符合技术要求,国产化齿轮箱与国外引进箱体相比具有内部组织致密,铸件本体屈服强度高、尤其是延伸率和冲击韧性更高的优点,确保了使用安全可靠性。
但国产化齿轮箱体外观质量与国外相比还存在一定差距,尚需进一步提升。在不久的将来,随着动车组齿轮箱制造技术平台的不断完善,中国动车组齿轮箱将完全代替国外品牌。
参考文献
[1]徐贵宝,沈本瑜.高强度铸铝合金在高速列车转向架上的应用[J].机车车辆工艺,1997(6):1-4.
[2]米国发,文涛,龚海军.Al-Si合金Sr变质研究现状[J].航天制造技术,2006(4):49-52.
[3]董秀琦.低压及差压铸造理论与实践[M].北京:机械工业出版社,2003:15-60.
[4]翟学金,金国宝.铸造铝合金ZAlSi7MgA处理工艺的优化设计[J].江苏大学学报,2002(4):57-59.
[5]徐贵宝,曹健峰,朱正锋.中国铁路关键铸钢件生产质量控制[J].铸造,2010(9):973-976.